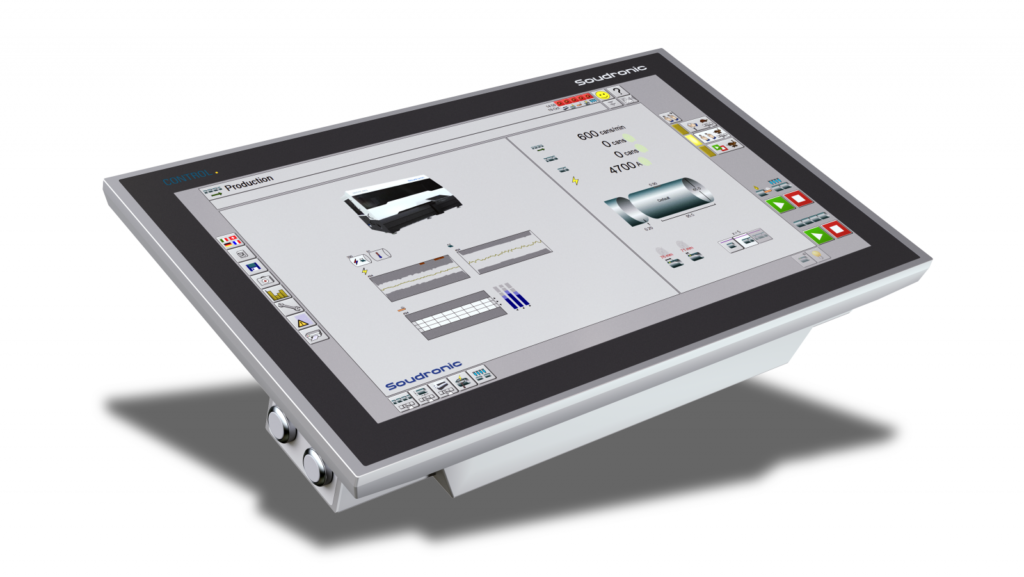
A 30-year success story – UNICONTROL
Back in the early 1990s, Soudronic began developing its AFB/FBB series. Designed to weld an unprecedented 1000 can bodies per minute, the machines placed enormous demands on control system response times and processing speed and outstripped the capabilities of all commercial systems available at the time. Seeing no alternative, Soudronic decided to create a solution of its own that would not only take the necessary speed in its stride but also reduce the wiring outlay and the variety of PCB hardware.
The result was UNICONTROL, a powerful, comprehensive platform that achieved these ambitious goals and came with several other persuasive features, including:
- a reduction in the PCB hardware requirement from more than 20 per machine to just five, making it easier for customers to manage spare parts
- an enormously high welding rate of 1100 can bodies per minute
- a distributed configuration featuring I/O boxes that communicated via a CAN bus and a vastly reduced wiring outlay, with electronics installed in the same locations as the actuators and sensors
- a welding monitor for all cycle rates, fully integrated into the control.
- a static welding converter from the first generation UNISOUD to PULSAR
Since then, and thanks to these improvements, we have been able to react flexibly to our customers’ evolving hardware and software requirements at any time. At that same early stage, we also ensured our independence from major control suppliers. The system’s success persuaded us to deploy UNICONTROL on many of Soudronic’s machines.
Time for a redesign
Ten years after the initial launch, the time had come for a first overhaul of the platform. From the outset, as always, our clients’ needs were the focus of all our efforts. We wanted to ensure the security of their investment, so backward compatibility for the PC boards was essential, and any modifications needed to remain affordable. From a technical perspective, the increase in CAN bus speed was central to the redesign. The industrial computers in the machines were equipped with the then state-of-the-art Windows XP operating system, and the electronics boards featured SMDs (surface-mounted devices). Even today, the revised system is still used to upgrade machines from UNICONTROL 1 to UNICONTROL 2.
Ongoing evolution
As the first decade of the century came to an end, the layout and design of the I/O units, most of which were based on UNICONTROL 1, were beginning to show their age. We thus decided to embark on the next generation in 2010, culminating in UNICONTROL 3, which is still in use today. Due to changing market needs, UNICONTROL was also made Internet-capable.
Another major improvement was the reduced size, thanks to the progress in electronics that we see reflected in today’s cell phones. It also meant an increase in power and a further reduction in the wiring outlay. There has likewise been a massive reduction in the number of variants required of the electronics boards. Today’s central components comprise just three electronic printed circuit boards. Their small size and highly integrated design still represent a production and testing challenge but have also increased batch sizes significantly. As a further advantage, it has also made the development, acquisition and operation of new test systems and adapters viable.
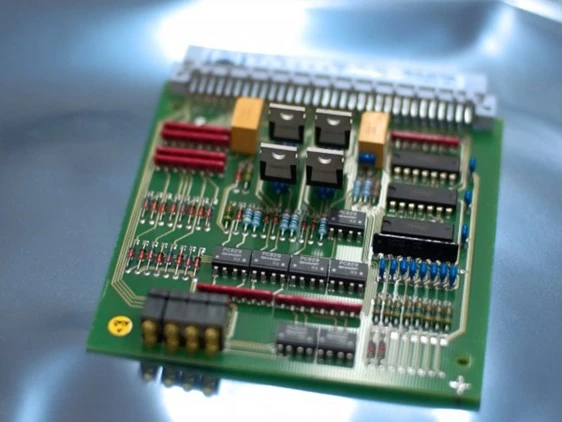
What does the future hold?
Predicting future developments is never easy, but we are already in a position to integrate the next generation, UNICONTROL 4, into our latest welding machines. As always, interoperability with older legacy systems has been a priority. Thanks to upgrades and conversions, the new components, with their improved performance and long-term availability, will combine perfectly with older machine generations. Choose a Soudronic system, and you are guaranteed a state-of-the-art system backed by comprehensive servicing and maintenance, equipped to handle your changing needs and strengthen your position in increasingly competitive market conditions. Perhaps most importantly, you have opted for a company with a single stated objective: to develop the technology that keeps you ahead.
The comparison UNICONTROL versions lists the different features of UC1, UC2, UC2+/UC3, and UC4.